Procedural Design for Robots
While designing the whole virtual production for the project, I filled multiple roles, from concept to design development, documentation was iterated and updated instantly with each panel design. I also generated all files sent to the robot, operated and cleaned the robot cell. A one man design team!
This was a proof of concept on how a project can be delivered as efficiently and effecticely as possible using great design thinking and parametric design.
I also had to learn robotic operation and programming in a month, which wasn’t easy.

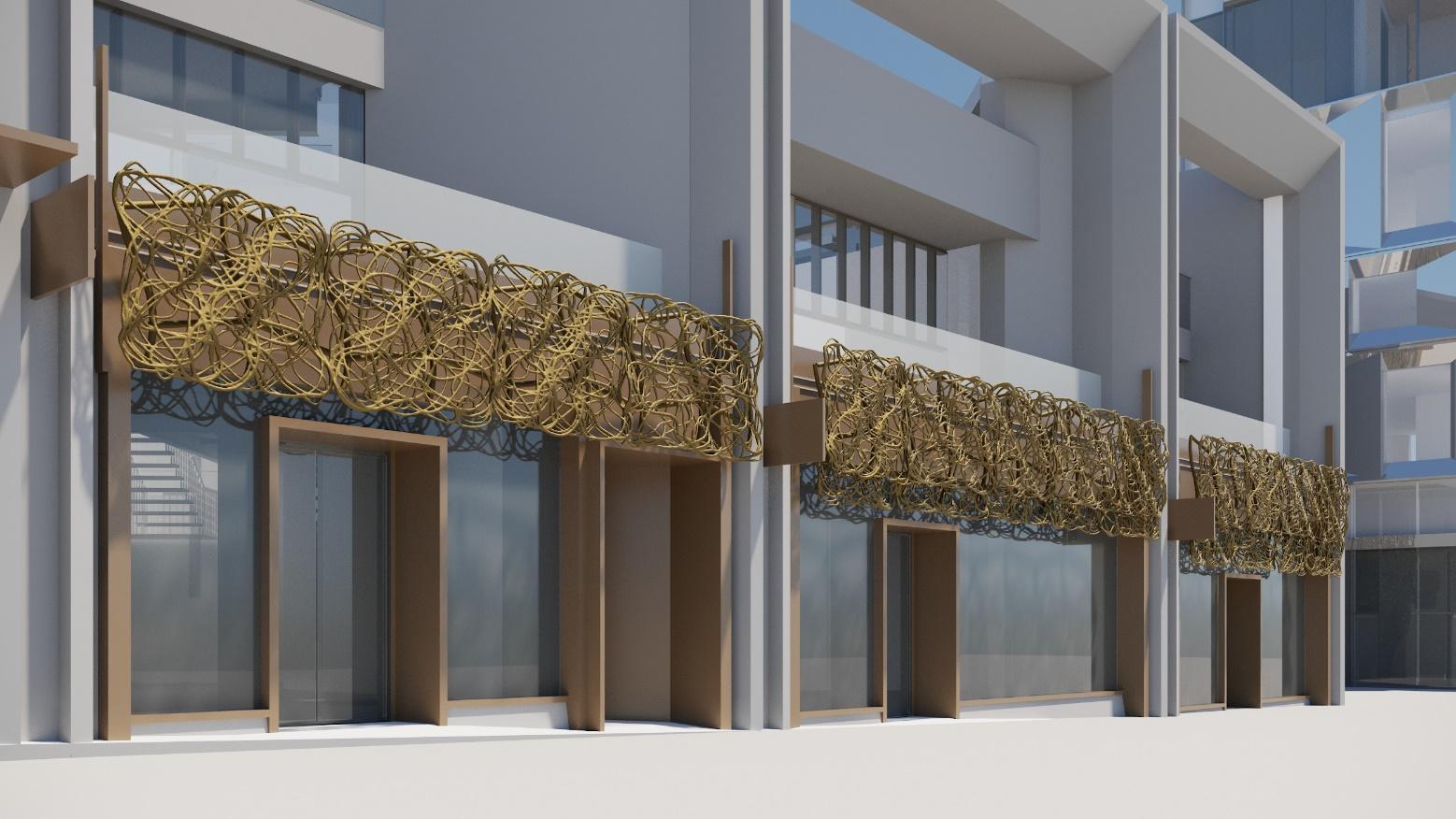
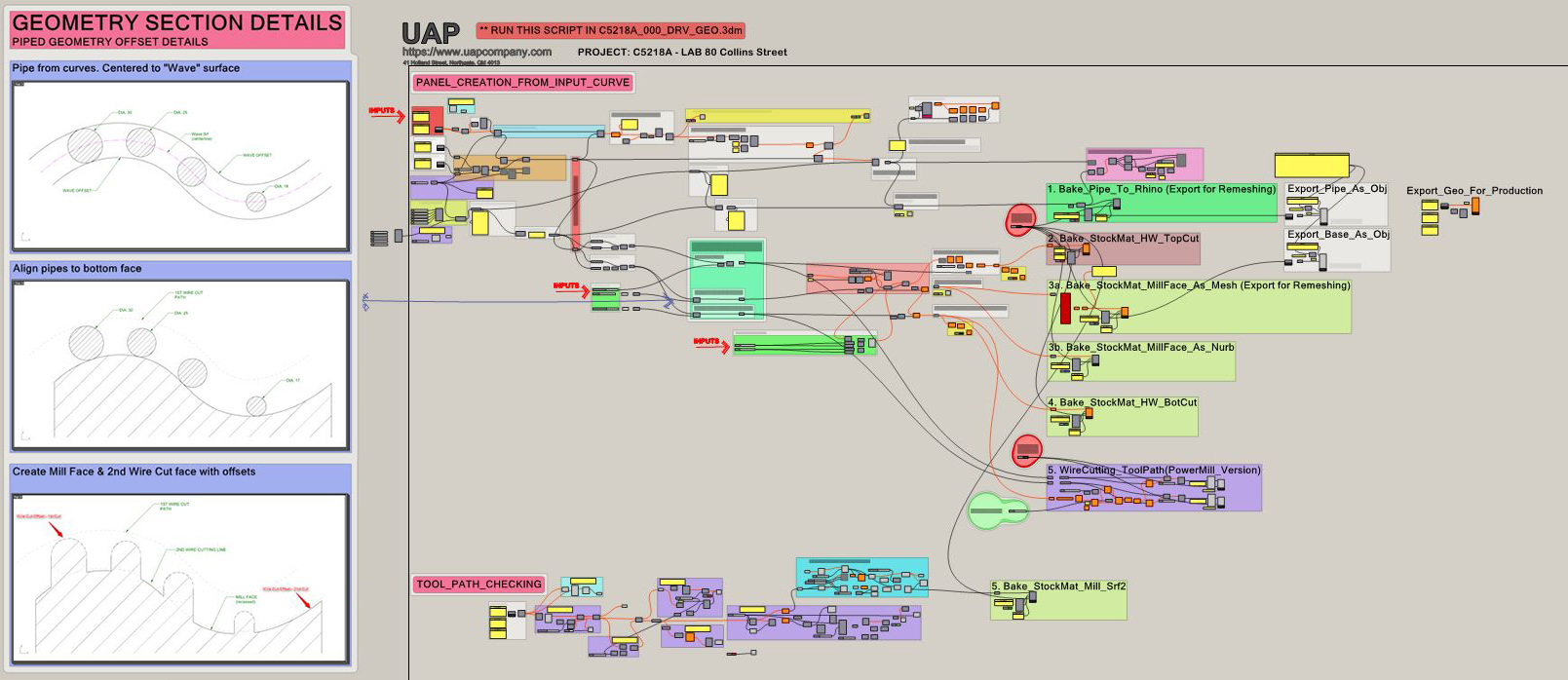
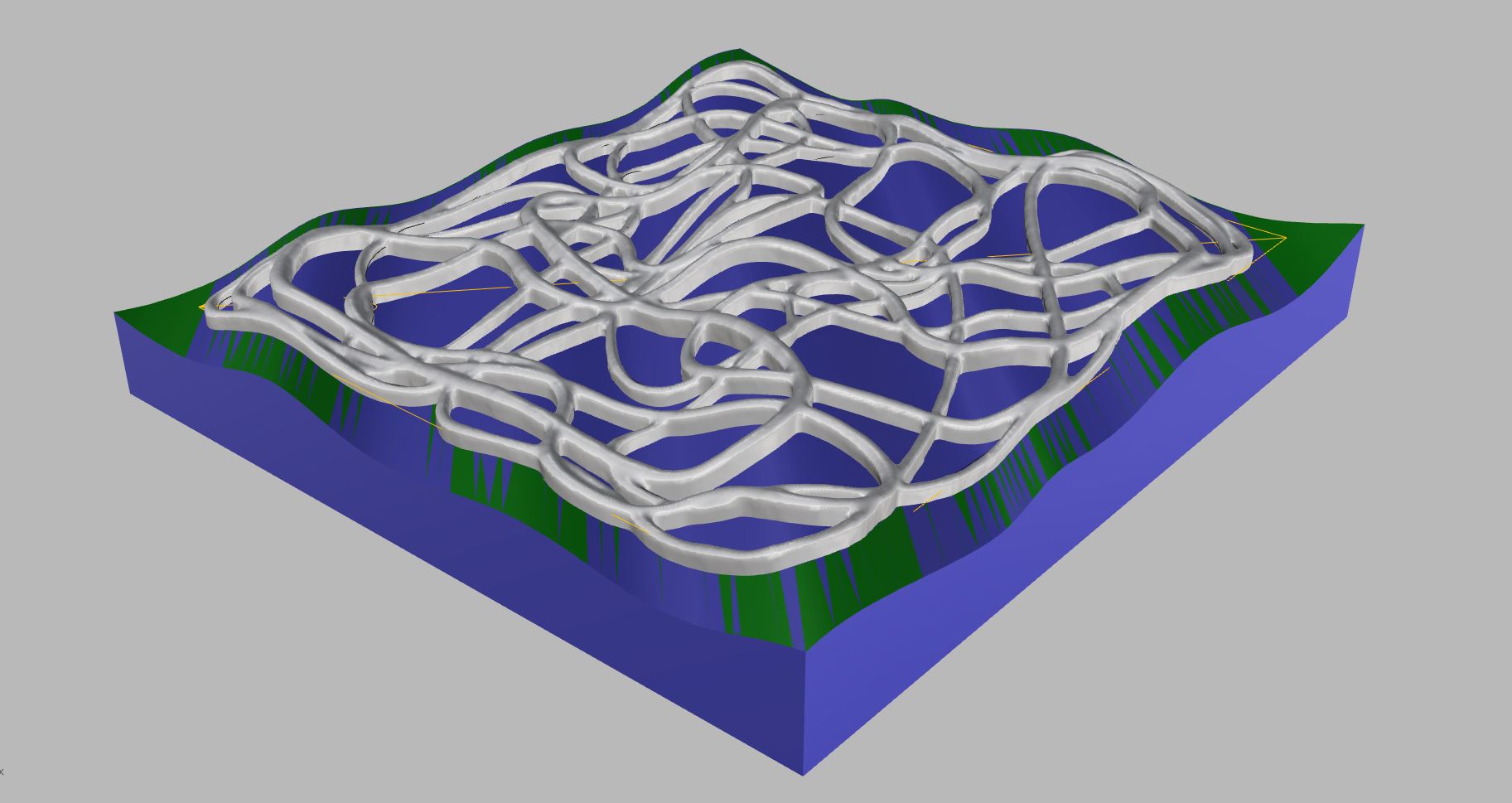
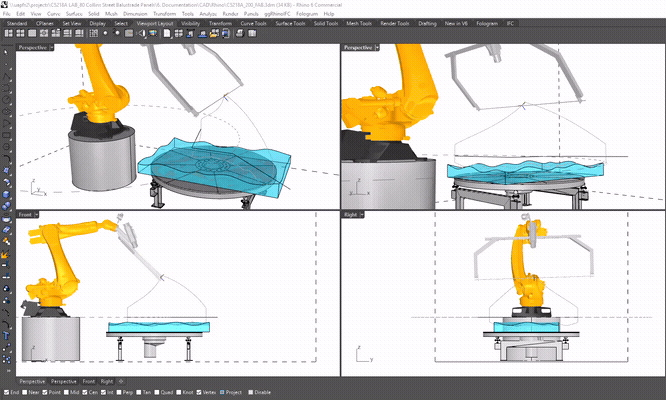
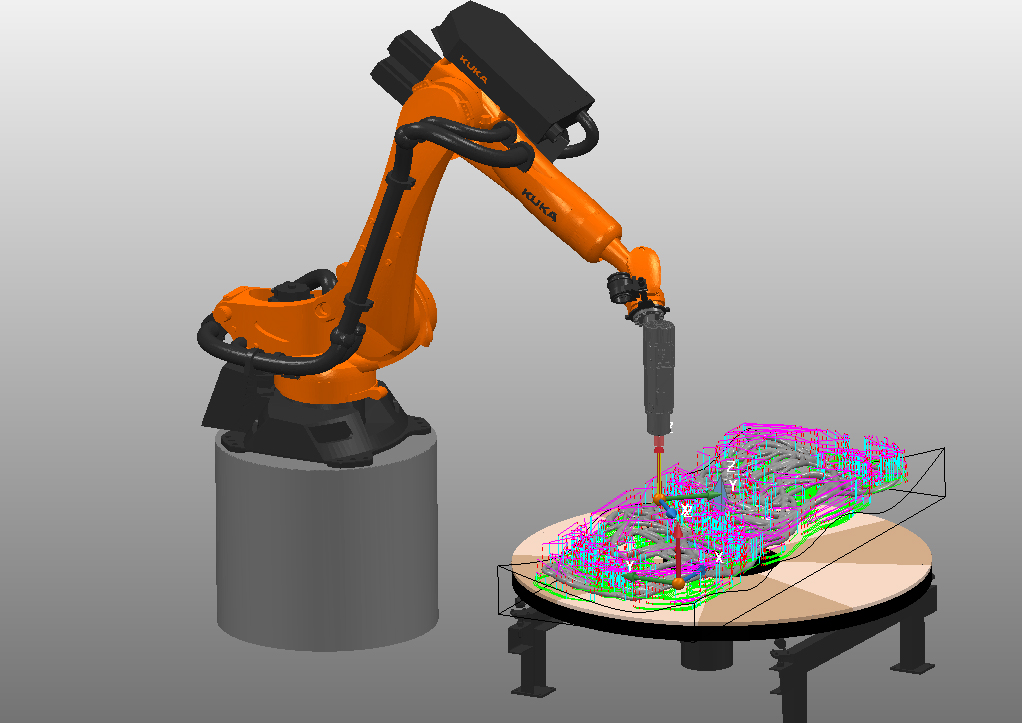

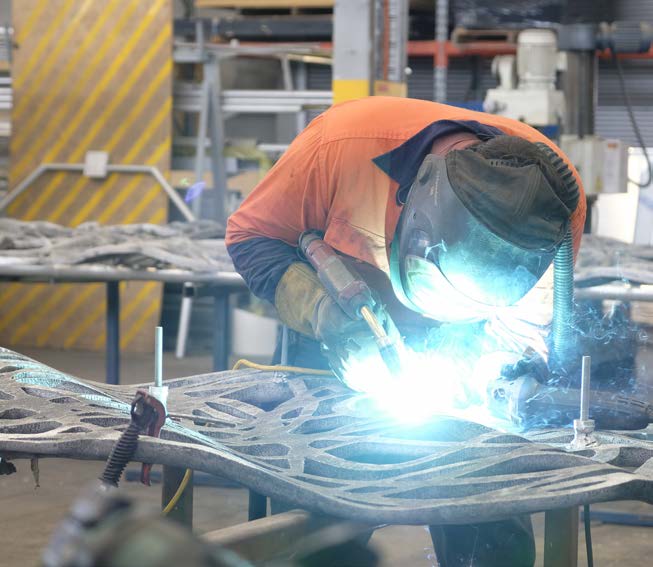
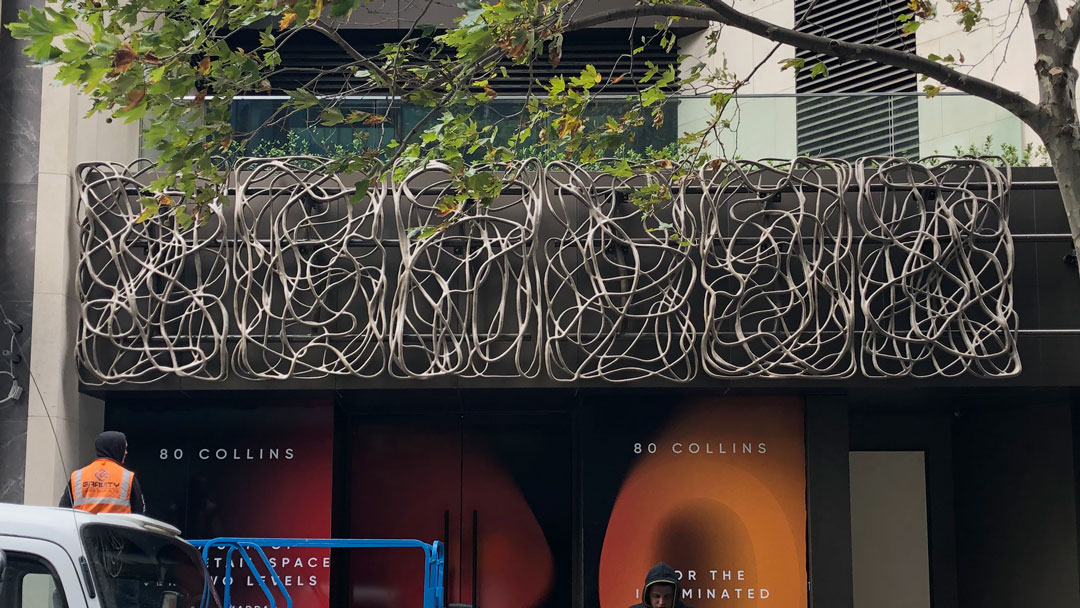
Digital Twin Aided Design
We leveraged 3D laser scans of the as-built wall, compared them with the original CAD setout points, and through Andy’s adaptable and very clever mounting system, were able to simplify the install of the artwork, all with the confidence and precision of our digital twin artwork.
Thanks Stainless Aethetics for giving us a shot at this project, incredible fabrication as usual!
observation:
While the use of digital twins are becoming more common, this sort of design thinking isn’t being used nearly enough in construction.

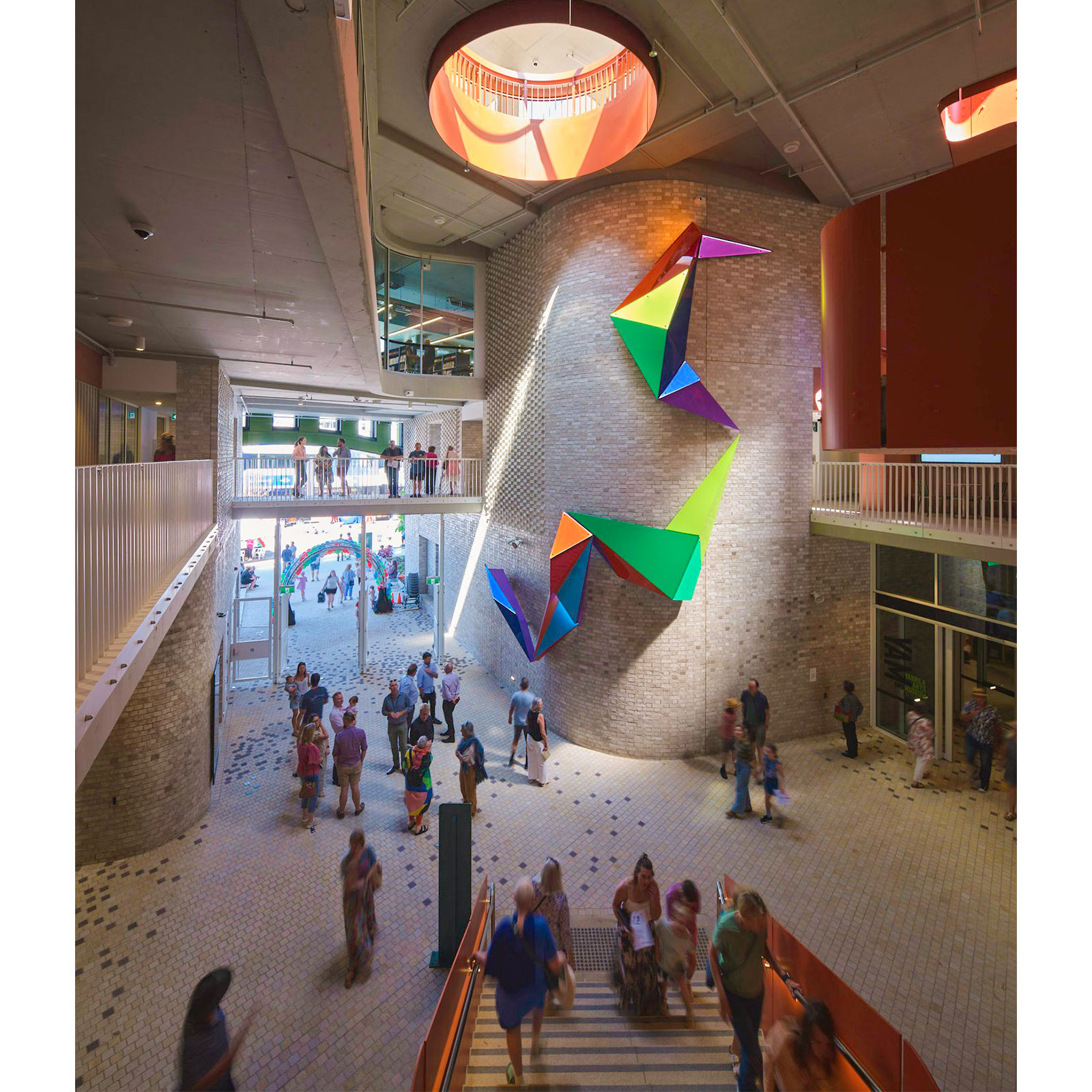


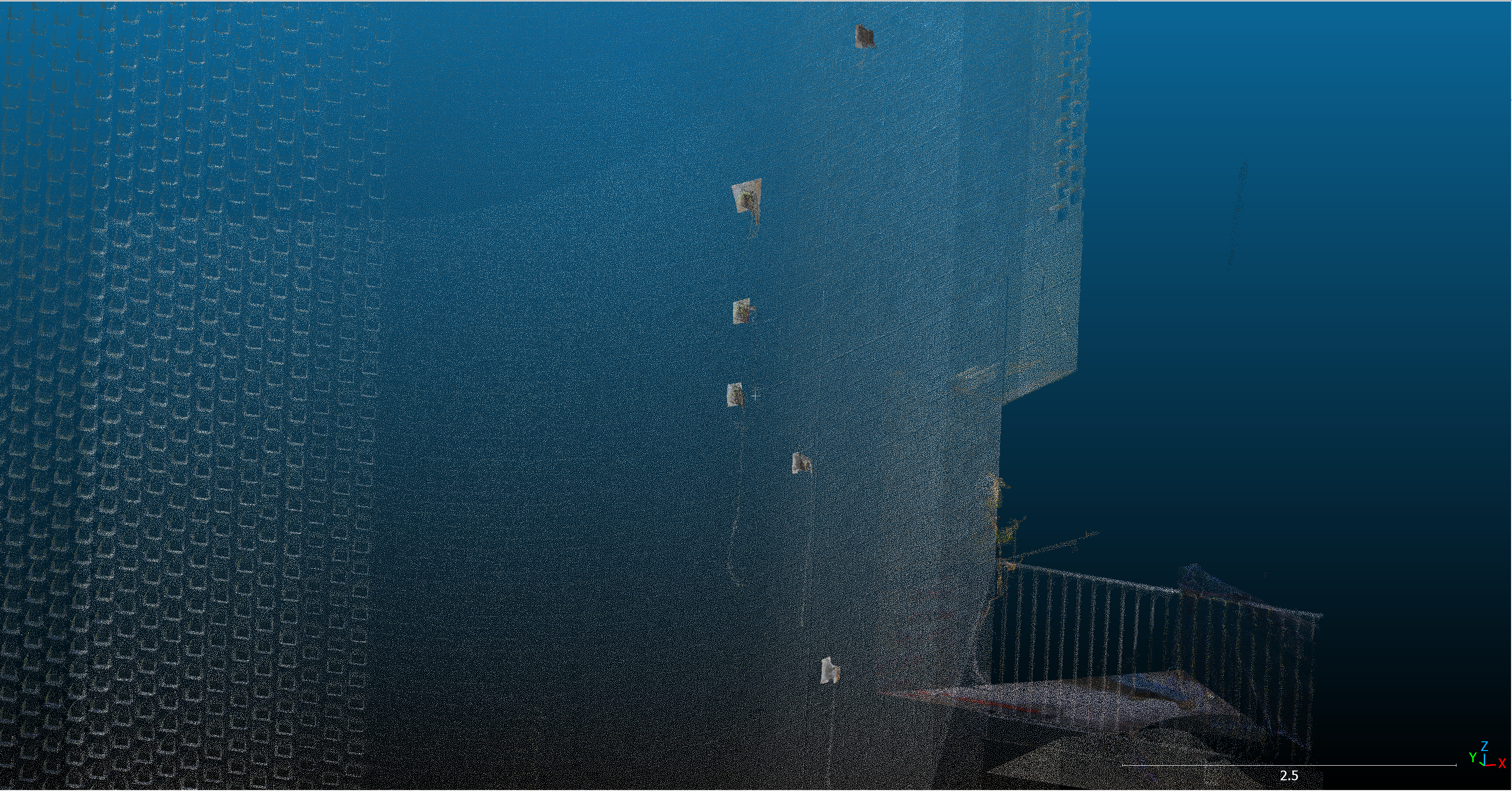


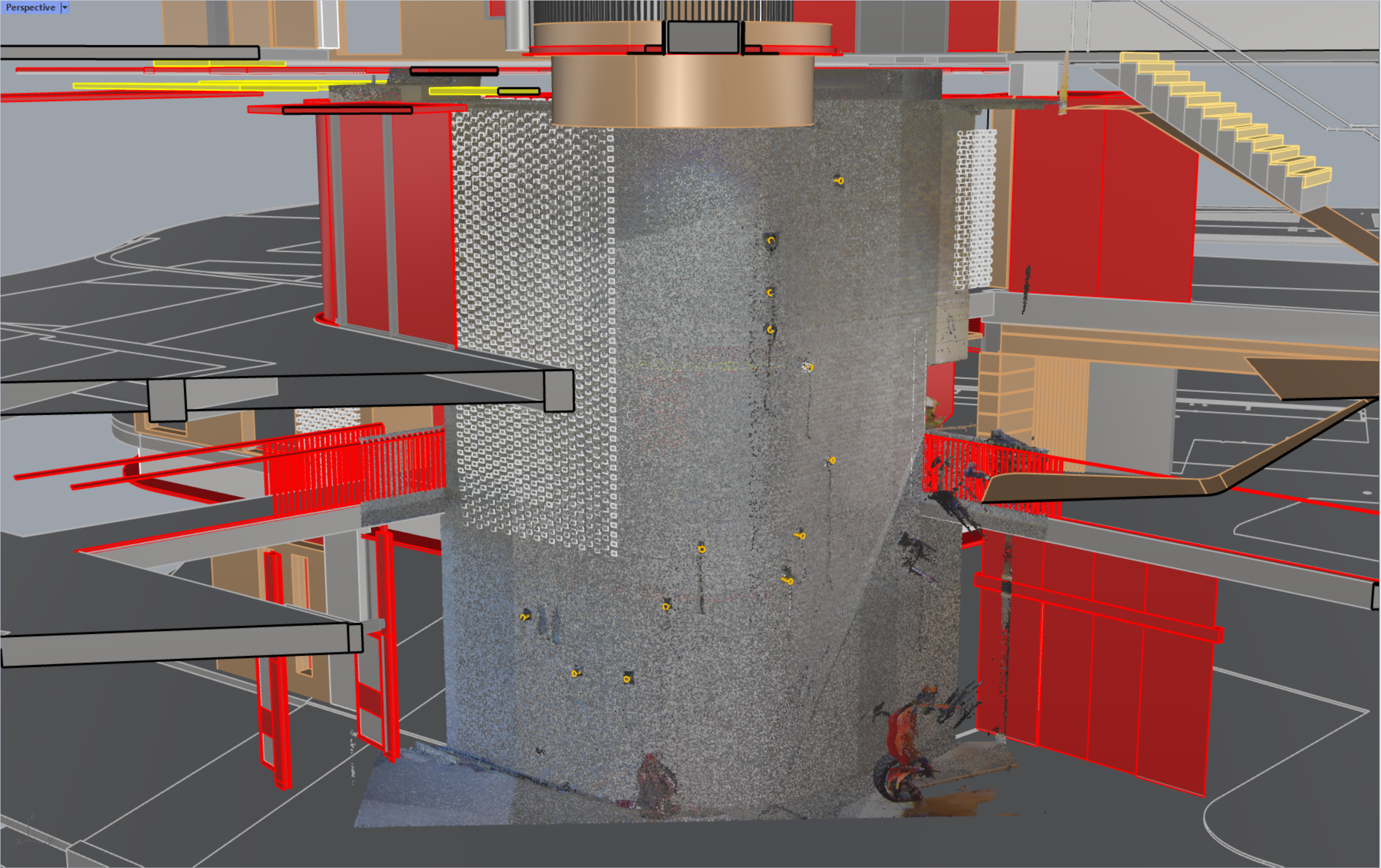
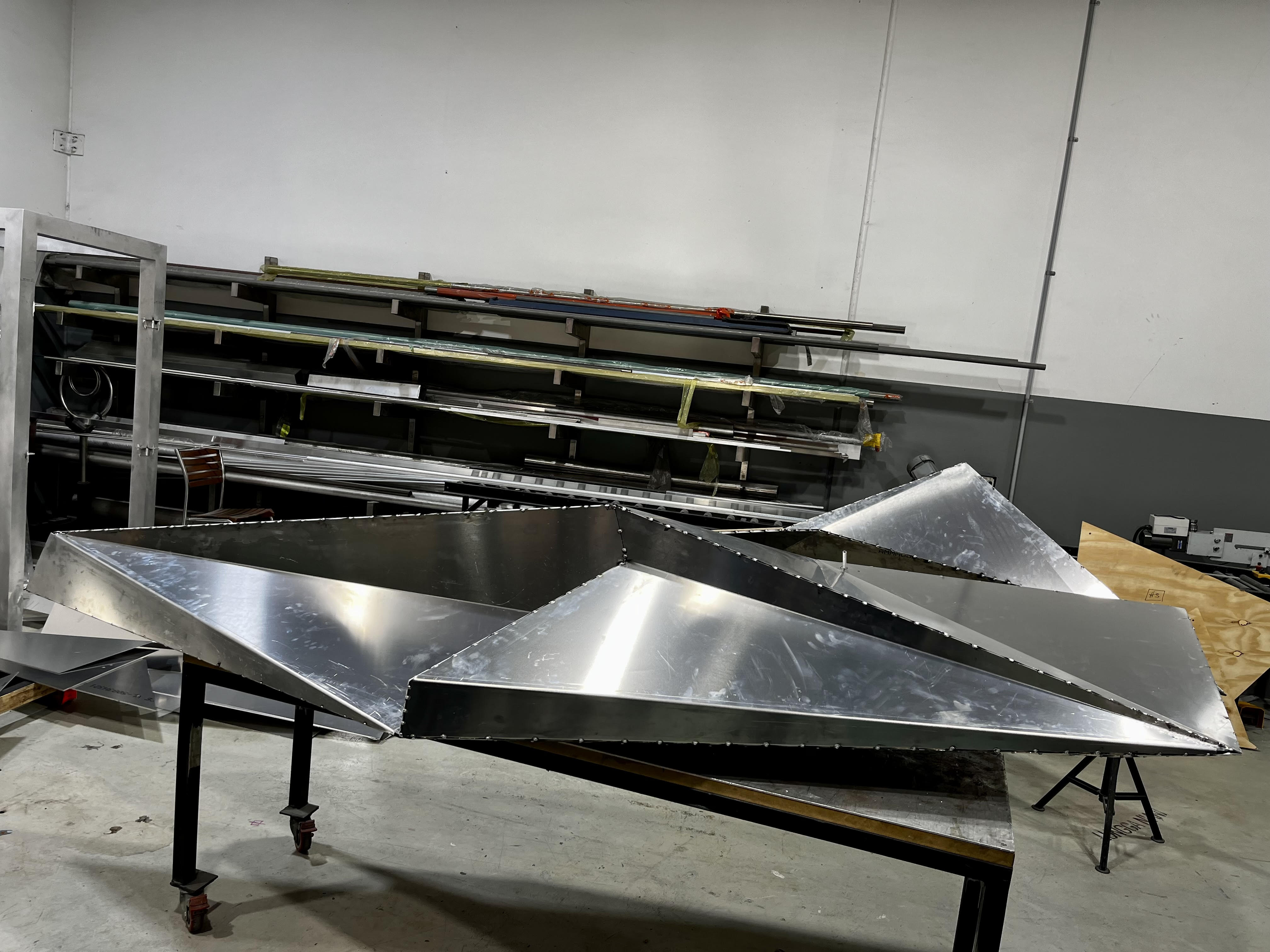
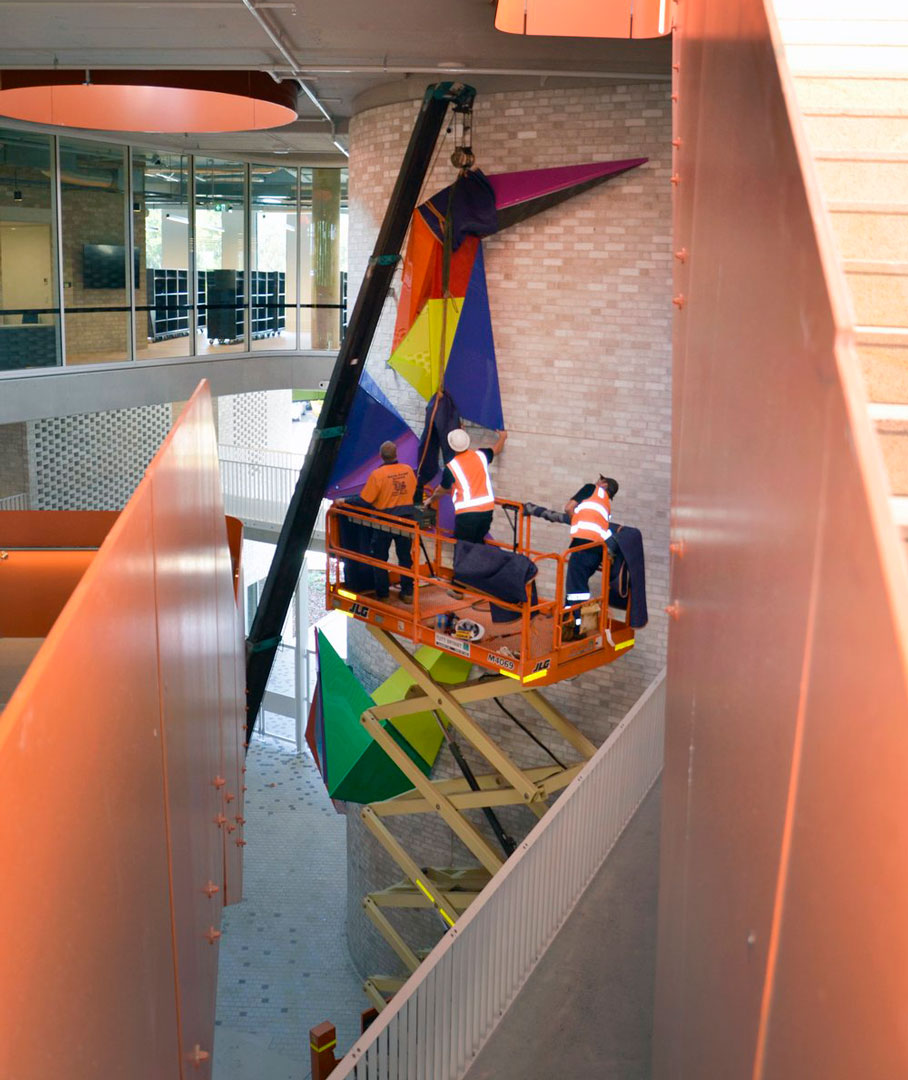
Big BIM data handling
Using a BIM model of 80 Ann street, Brisbane, which contained all electrical, fire services and elevator details, I was able to segment and bring the CAD model into Houdini for poly reduction, UV cleanup and ultimately collapsing parts by material, so that the result could easily be brought into the Unreal engine for visualization (and VR!!!).
In the past, this process would usually take days of processing via multiple software packages, but with Houdini and a few attribute tricks, this only took a few hours.
I also leveraged the Cesium plugin to locate the building in Google 3D Maps Tiles for context. A week’s work in a matter of a day.
Stats
- 1.2 GB BIM model (19 embedded working files)
- 700k objects condenced down into 75 meshes with material data
- 32 million polys down to 4 million (unfortunately the fire service piping didn’t make the import due to too much detail)
- All processed on a laptop with 32GB of RAM (unheard of 5 years ago)
- Ceveat: Mesh only data, I’d need to impliment a Rhino/Grasshopper workflow for dealing with solids/surfaces



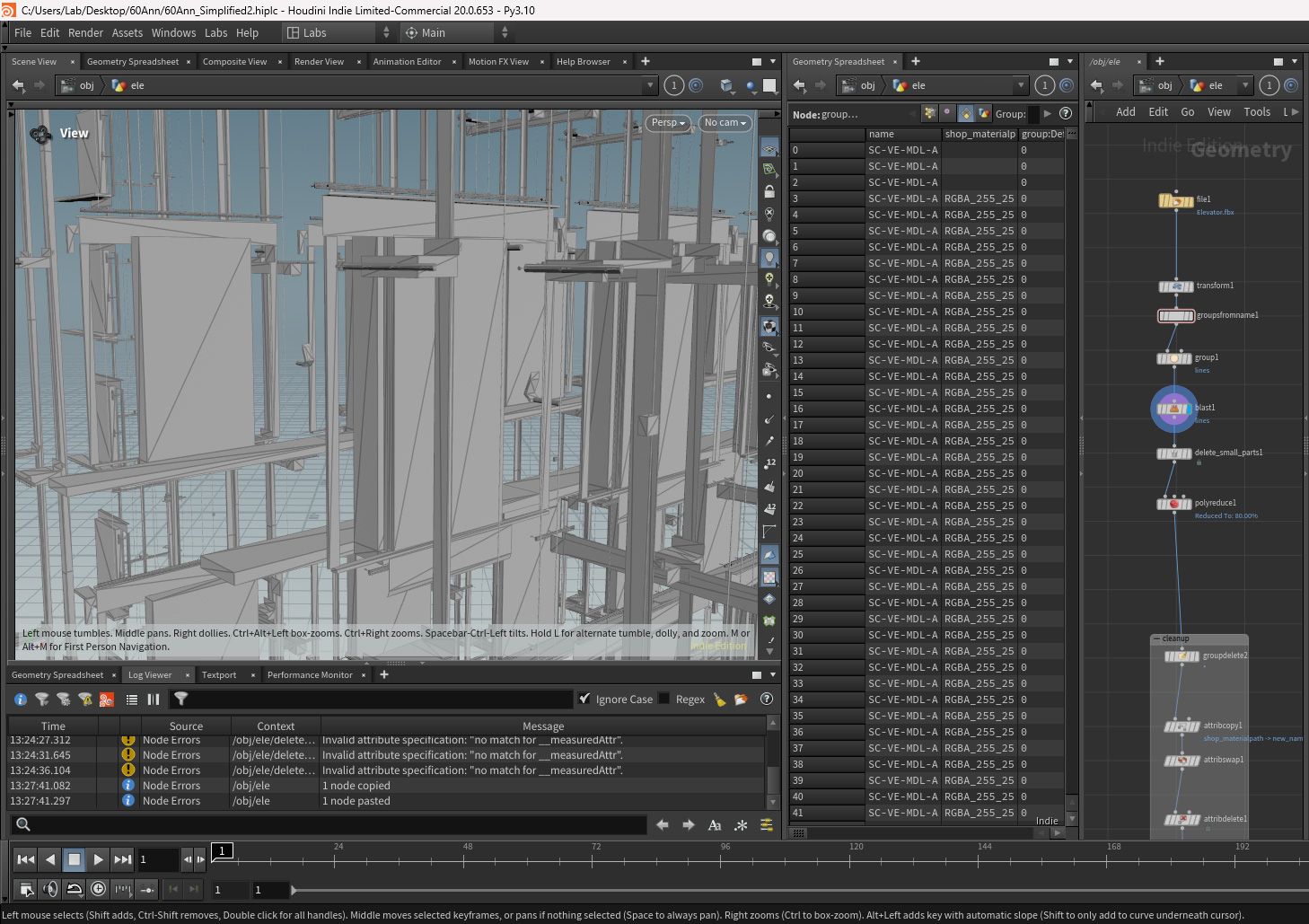
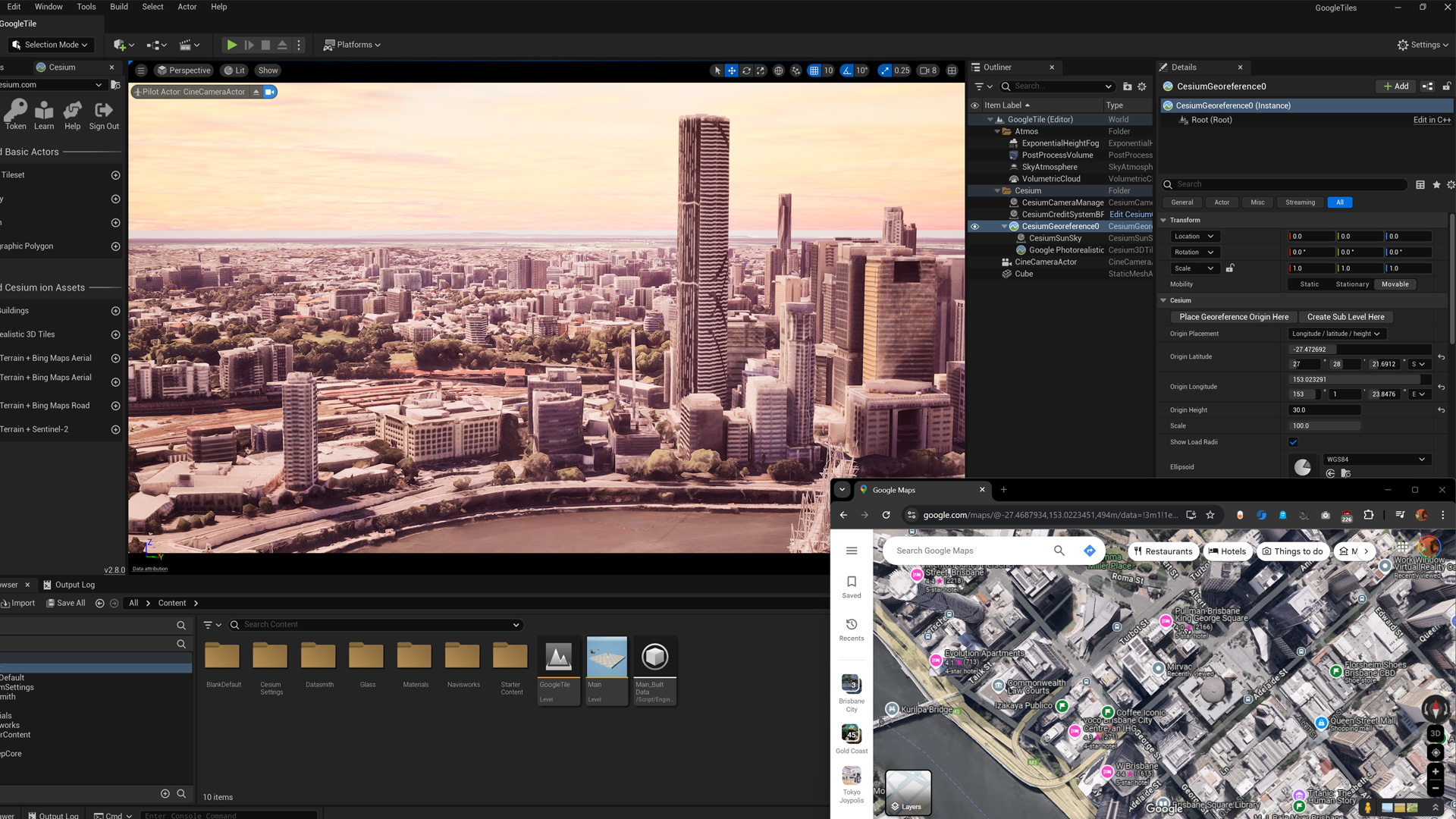
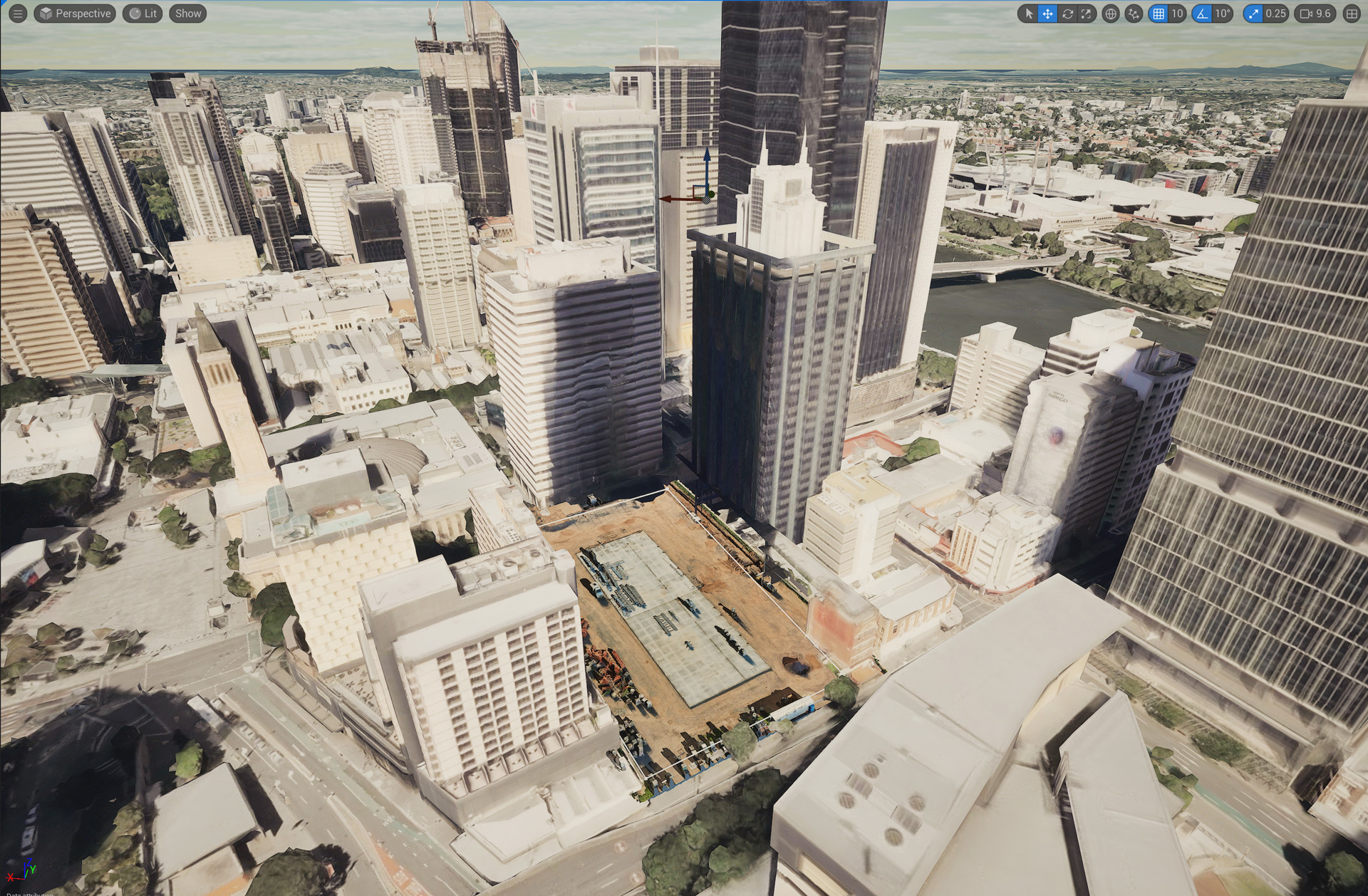

VR Design / AR Assembly
This artwork, “Flourish” by Katrina Tyler was used as a casestudy for digital prototyping in VR and hololens aided assembly on the workshop floor.
Due to restrictions in hand entrapment and climbability, each totem needed to be designed to minimise certain sized gaps between modules. VR placement was used as a quick alternative to placing each piece on the computer screen.
This was also the first time I would have to train up one of the workshop workers to use the hololens in the assembly and tack welding process.
While there was a bit of troubleshooting needed, the case study was a huge success, saving many labor hours reading off workshop drawings.
The perfect project for VR/AR implementation.
Project details
Design Robotics
UAP
Due to restrictions in hand entrapment and climbability, each totem needed to be designed to minimise certain sized gaps between modules. VR placement was used as a quick alternative to placing each piece on the computer screen.
This was also the first time I would have to train up one of the workshop workers to use the hololens in the assembly and tack welding process.
While there was a bit of troubleshooting needed, the case study was a huge success, saving many labor hours reading off workshop drawings.
The perfect project for VR/AR implementation.
Project details
Design Robotics
UAP


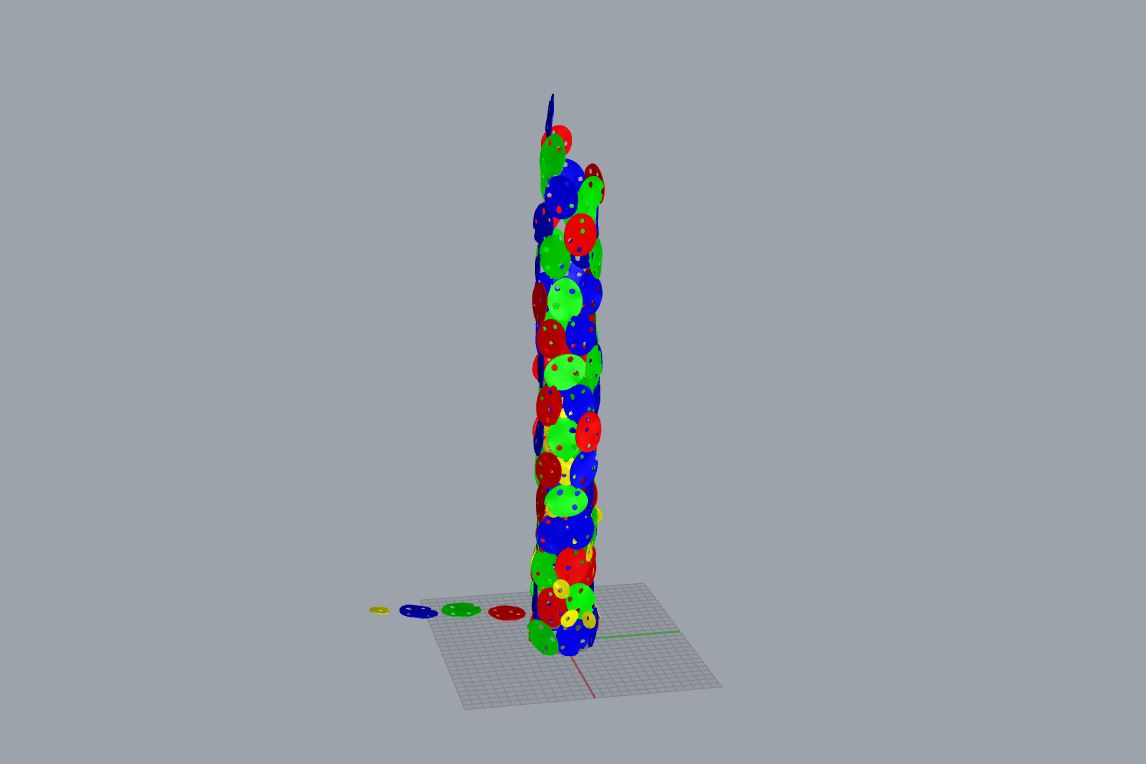

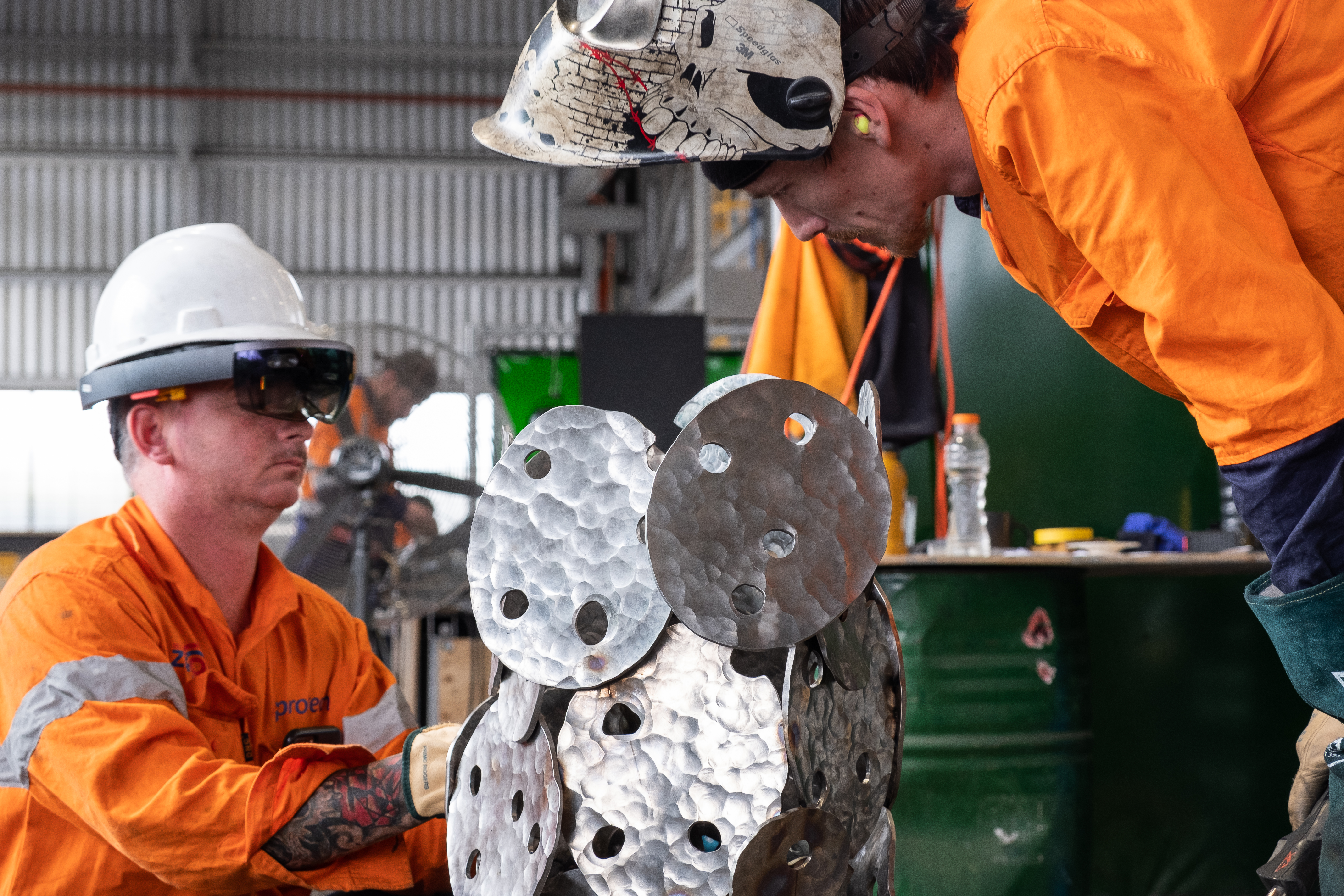
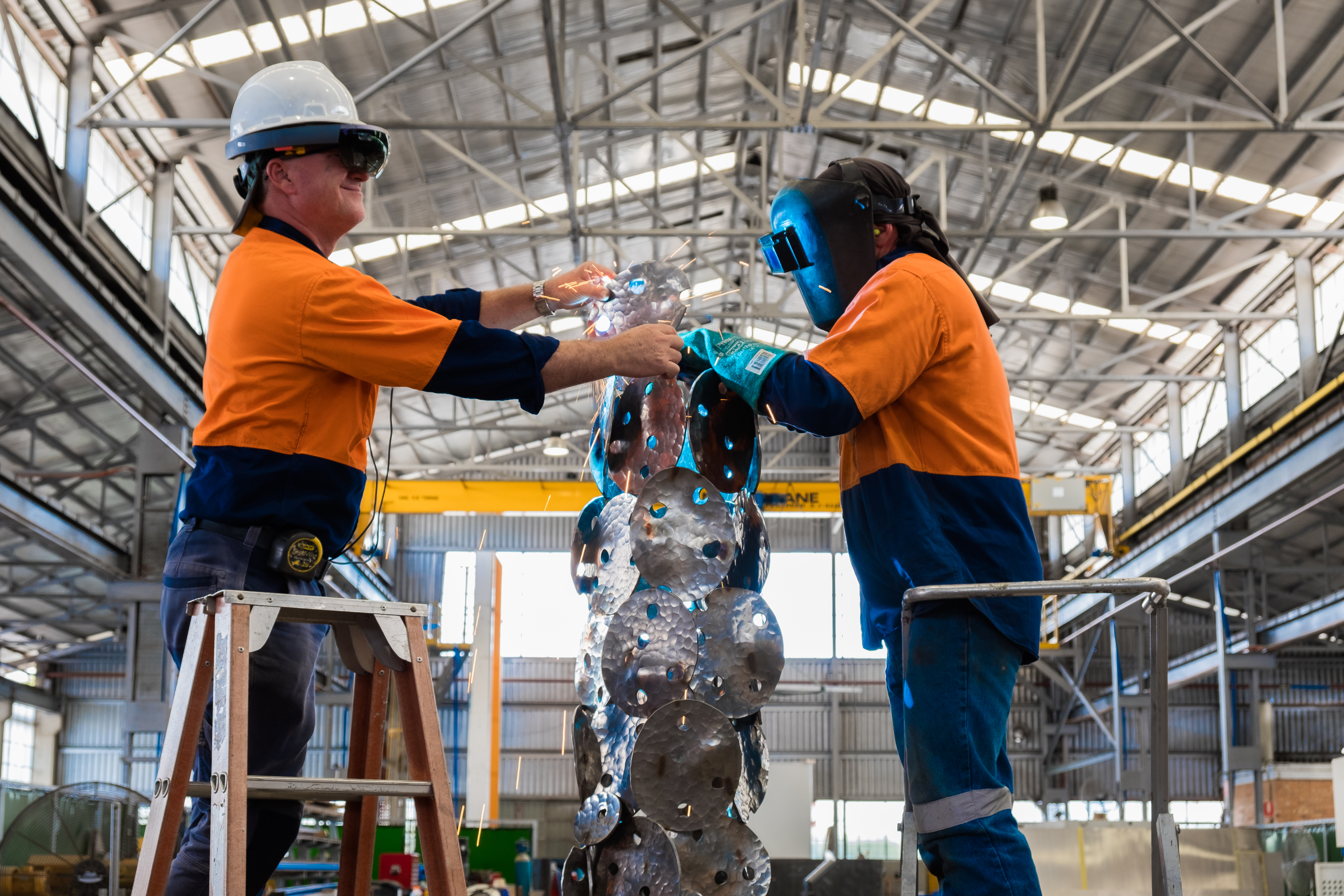

Augement Assembly Fabrication (ARfab)
The task was for me to align the virtual CAD model with all the drill holes and IDs with the real fabricated main structure, and mark out the hole locations for the workshop guys to tack weld over 500 varied length rods.
This was my first taste of using the hololens on the workshop floor, so I was never really certain it would actually work. With a little patience, a smart approach and a whole lot of luck (the hololens did a fantastic job of tracking/anchoring the main structure, I honestly thought it was going to fail) I managed to do the job quicker than the traditional method of working off workshop drawings.
A lot of labour hours saved!
Project Details
Design Robotics
UAP
Interview
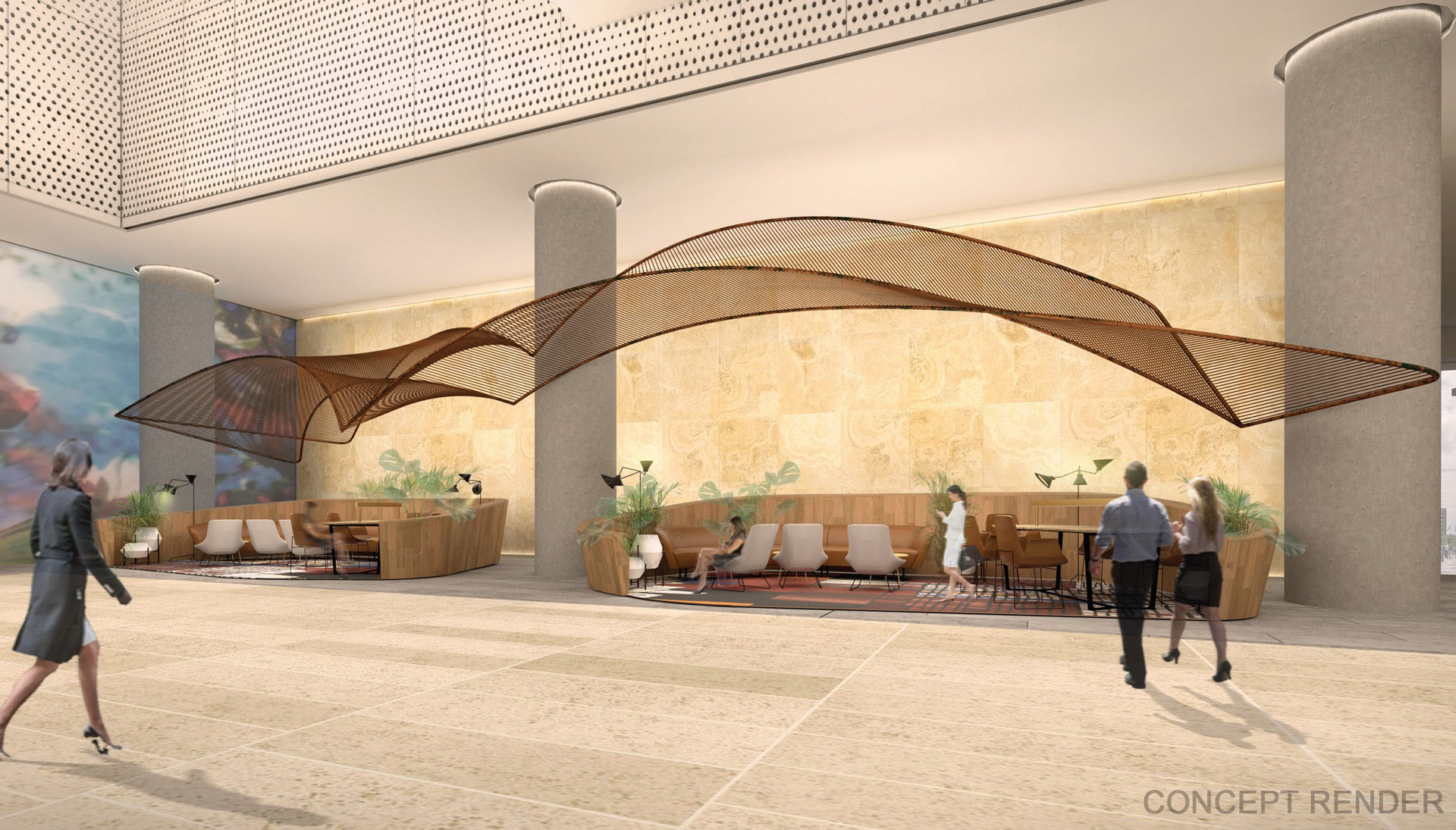


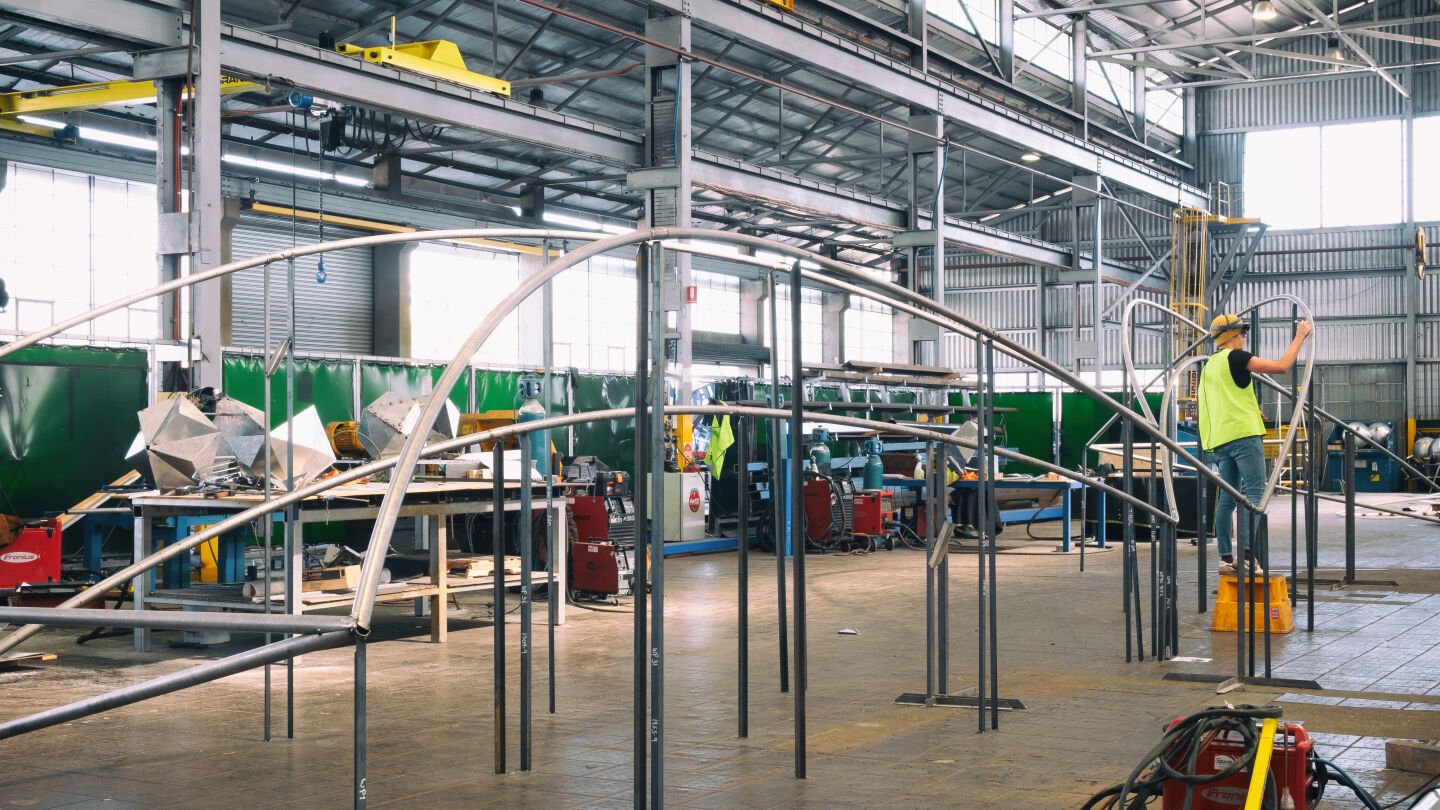


